Постоянно растущие требования по уменьшению размера помола угля неизменно приводят к увеличению уровня абразивного износа помольного оборудования.
Существует ряд систем, которые используются в процессах дробления угля для ТЭС / ГРЭС.
Частями, которые поддаются абразивному износу на участках помола, являются помольные валки, помольные тарели и пружинные механизмы.
Помольные валки или колеса и помольные тарели или столы производятся из различных видов чугуна.
Наиболее часто используемыми материалами являются Ni-Hard I, II, IV, или их апробированные эквиваленты.
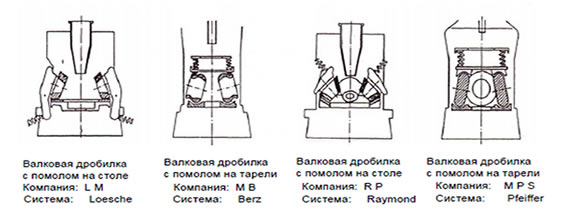
Рис. 1: Системы машин, используемых для дробления угля.
На рисунке 1. показаны различные дробильные системы, которые используются на ТЭС / ГРЭС. Уголь подается на помольную тарель / стол и измельчается под воздействием давления валков, создаваемого высоким трением, и характеризуется низким уровнем ударного износа между валками и столом / тарелью. Этот износ создает шероховатую и
неровную поверхность как на валках, так и на тарели и уменьшает тонкость помола, значительно уменьшая эффективность ТЕС / ГРЭС. На стадии, когда машины работают в режиме минимальной эффективности, которая также является максимальной величиной допуска, из-за износа наглядно можно увидеть изношенность рабочих механизмов.
В прошлом в литературе говорилось, что невозможно обслуживать, осуществлять наплавку этих типов стали. Совсем недавно стало возможно производить твердосплавную наплавку чугуна с получением великолепных результатов.
Восстановление этих валков твердосплавной наплавкой по сравнению с заменой на новые валки открывает интересные экономически выгодные возможности для отрасли.
При сравнении общих затрат для обеих опций, замена с использованием наплавленных валков приносит экономию затрат около 40%. Но, наплавленные валки имеют более длительный срок службы, чем сделанные из Ni-Hard.
Принимая во внимание ? 10% больший срок службы, чем у новых валков, общая экономия затрат составляет 67%.
Подготовка поверхности:
Чугунные валки и тарели, которые требуют восстановления поверхности, должны быть подвержены испытаниям на проникновение жидкости (PT crack test). Перед тем как начинать наплавку, необходимо очистить базовый материал от трещин. Это значит, что необходимо зашлифовать большие трещины или полости. Не зависимо от объема пористостей, любая определяемая пористость в сплаве Ni-Hard, не будет пагубно влиять на сокращение срока службы наплавляемой детали.
Наплавленный сплав, противостоящий абразивному износу минералами, относится к твердым сверх- эвтектическим ледебуритным чугунам. Функция углерода состоит в том, чтобы сформировать первичные карбиды в форме M7C3 и MC. Однако, стойкость к износу из-за объема карбидов, размера и твердости, а также, твердости основы . Мы имеем ряд сплавов DURMAT, которые относятся к группе твердых сверх-эвтектических ледебуритных сплавов, в качестве порошковой проволоки для твердосплавной наплавки чугуна, угольных / цементных мелющих колес / валков, тарелей / столов.
В зависимости от процесса наплавки и анализа наплавленного слоя, наш опыт подтверждает, что срок жизни может быть и больше, чем на 10%. Фактически было достигнуто увеличение срока службы в 2 – 3 раза выше, чем у валков из Ni-Hard в зависимости от чистоты угля.
Применение сплавов при помощи материалов DURMAT FD 55, DURMAT FD 60, DURMAT FD 65 или DURMAT FD 70 позволит получить в микроструктуре наличие большего количества и меньших размеров первичных карбидов Хрома, чем в микроструктуре чугуна (например, в
сплавах Ni-Hard). Именно по этой причине наплавленные детали из чугуна будут иметь более высокий срок службы по сравнению с не наплавленными.
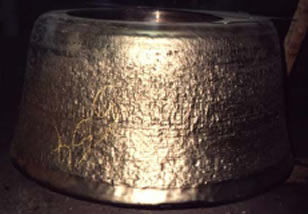
Рис. 2
Однако важно также отметить, что сплавы с высоким содержанием Хрома улучшат свойства стойкости к износу по сравнению со сплавами Ni-Hard, но все же будут содержать меньше карбидов хрома с меньшим размером зерен по сравнению с наплавленными сплавами на мелющих деталях из чугуна.
Ожидаемая эффективность наплавленных сплавов во многом зависит от процесса наплавки и его параметров. Это особенно важно, когда требуется наплавка в один слой.
Выбранный процесс наплавки прямо влияет на смешивание с базовым материалом, содержание сплава, развитие микроструктуры и таким образом, на стойкость к износу наплавленного сплава.
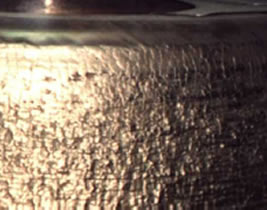
Рис. 3
Каждый наплавленный слой содержит в себе так называемые «качественные трещины». Эти разгружающие давление трещины необходимы и создаются умышленно в процессе наплавки. Они формируют неправильную модель поперек наплавленных бортов по всей длине валка или стола. Цепочка трещин очень четко проиллюстрирована на изношенных валках, представленных на Рис. 2 и 3. Мелющие валки, сделанные из Ni-Hard IV (размер: ?1100 x 500 мм), изъяты из использования после ?18000 отработанных часов (в зависимости от кусков, песка, зольности, и других включений). Они могут восстанавливаться без удаления оригинально наплавленных «качественных трещин». Это показано на двух рисунках, представленных ниже.
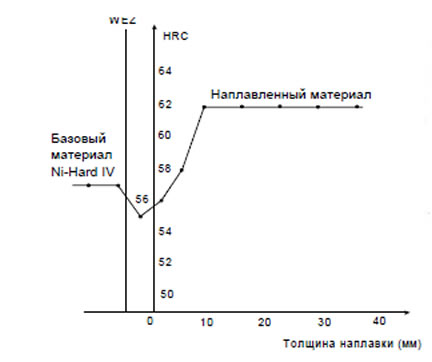
Рис. 4
Рис. 4 показывает разницу твердости (HRc) между Ni-Hard IV и наплавленным сплавом DURMAT FD- 60. Это четко показывает незначительное увеличение твердости в нескольких первых слоях с крутым уклоном до требуемой твердости.
Твердосплавная наплавка мелющих валков и тарелей в наши дни демонстрирует великолепные результаты и увеличение спроса в мире, а также, становится общепринятой практикой в европейской и американской промышленности. Она существенно улучшает срок службы, уменьшает время простоя, которое существенно уменьшает производственные затраты на обслуживание то ли на ТЭС / ГРЭС или в цементной промышленности, как и сокращение затрат для конечных потребителей.